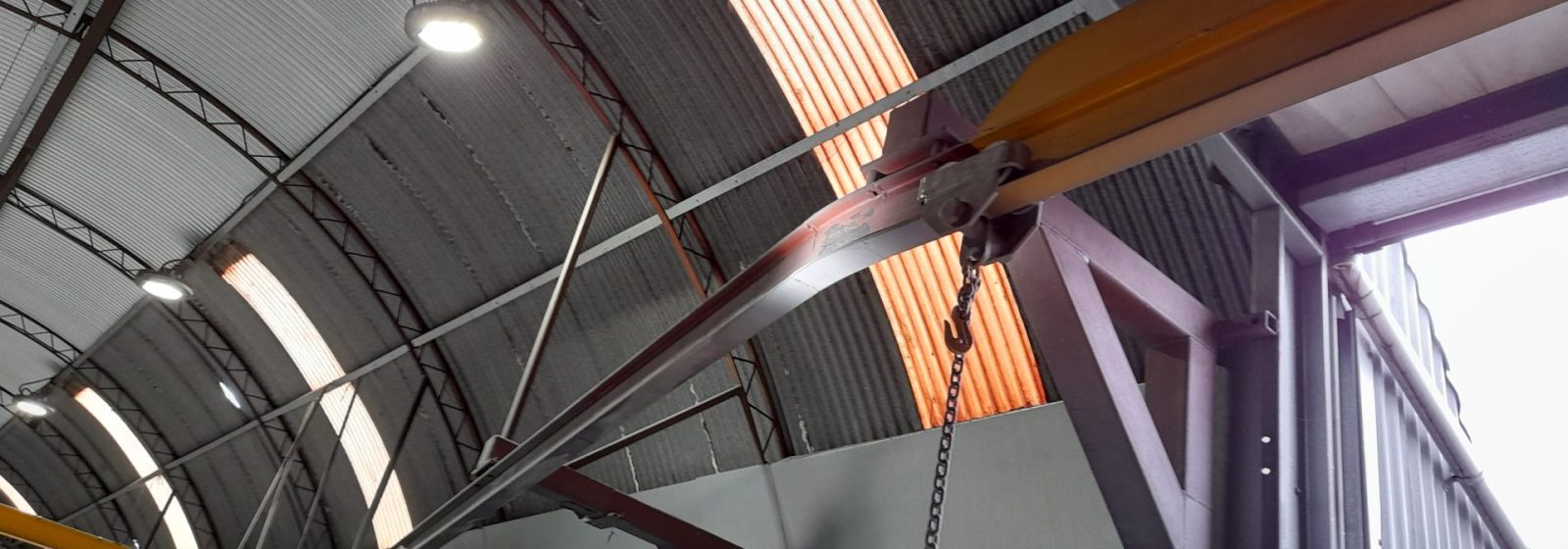
Monorail System
Made to measure – Customised strengthening of a paint line monorail system
Our client’s paint line monorail system – which carries steel beams through the paint application process – was first built over 20 years ago. Being an older structure it was uncertified, and didn’t comply with current AS/NZ design codes. GRIT was called in to design a strengthening scheme for this bespoke structure that would provide more structural capacity, keep operations personnel safe and be cost effective.
A multitude of challenges
There were several challenges to overcome, such as a lack of as-built drawings making it difficult to understand how the monorail or the building housing it were originally constructed. A shortage of space around the monorail would limit the upgrades that could be done. Replacing the weak main monorail beam wasn’t viable, as it would mean replacing customised parts of the monorail at unnecessary expense. What’s more the monorail needed to stay operational throughout the upgrades, meaning work could only be done at weekends, and had to be fast.
Modelling a customised solution
Our first priority was accurately 3D modelling the existing monorail, to give us a solid understanding on which to base our designs.
Rather than attempting to analyse the entire building which supported the existing monorail hangers, our team designed a strengthening solution that could withstand large point loads independently of the building. This approach simplified the design process and allowed detailed engineering sketches to be issued to the fabricator quickly.
Strengthening the monorail by site-welding a new steel member onto the existing main beam was the option preferred by our client. GRIT’s engineers designed this tricky solution to make use of commonly available steel sections and simple welding details that would speed up the work and minimise cost.
Because part of the monorail runs inside a container, site-welding would not be practical on that section, so GRIT’s solution also proposed stiffening the beam by connecting it to the roof of the container.
With a lack of information about the existing structures, the sound engineering judgement of our team came into play here. Working closely with the client and fabricator to come up with practical and innovative ways to stiffen the structure, our team was able to develop a solution that was appropriately conservative, without compromising cost effectiveness.
Cost effective and certified
The result for our client was a fit-for-purpose design that minimises cost and disruptions to their operation. We provided engineering sketches for fabrication, and helped to streamline construction by communicating directly with the contractor throughout the process. And because GRIT has Chartered Engineers, the structure can be certified as compliant with current building codes.